· Engineering · 4 min read
Torsion: Exploring the Twists and Turns in Applied Engineering
Torsion offers insights into twisting forces, critical for many applied engineering problems.
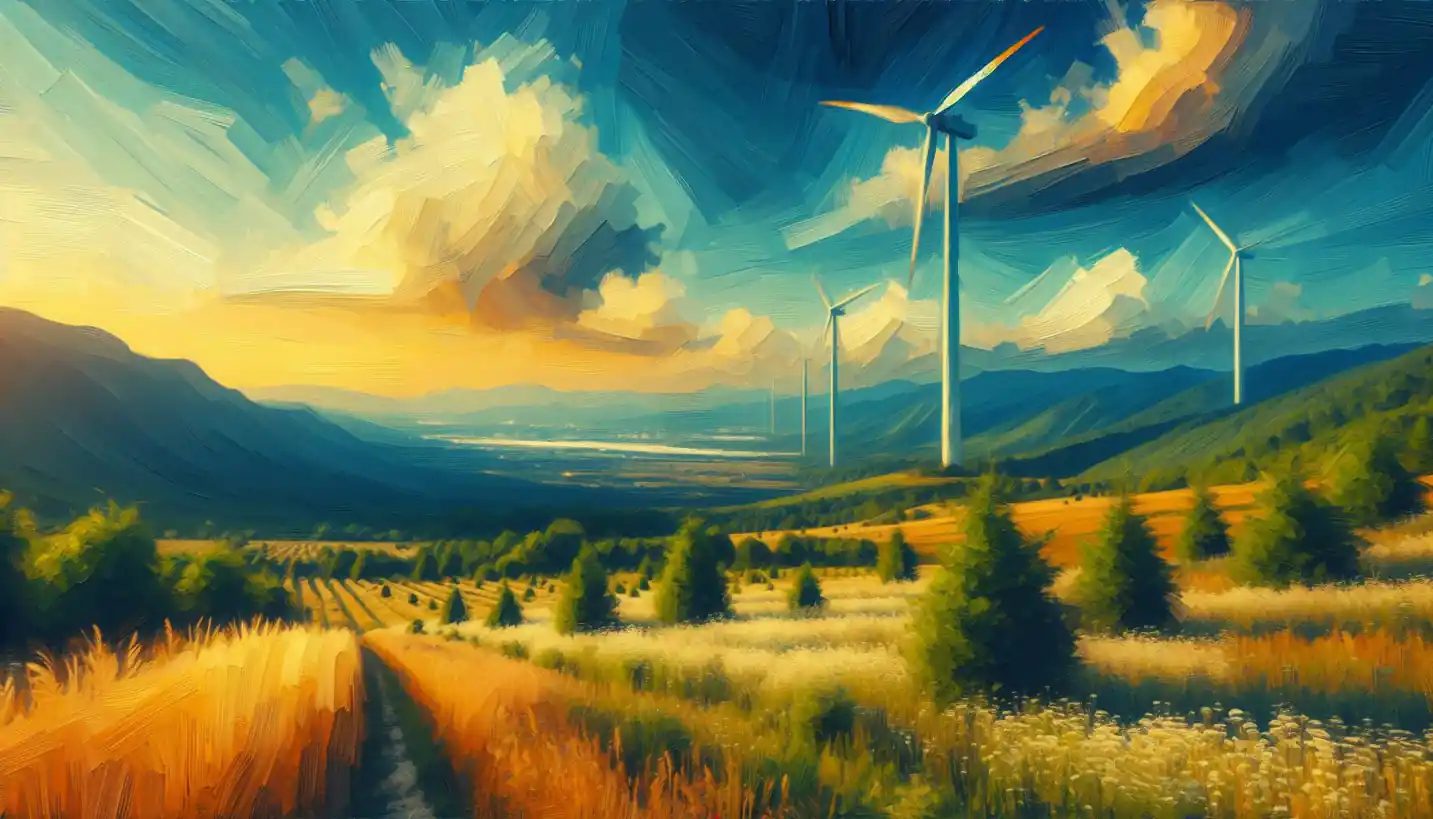
Have you ever held a rubber band between your fingers and twisted it? That simple act helps us understand a fascinating engineering concept called torsion. In engineering, torsion refers to the twisting of an object due to applied forces, and it’s a critical aspect in the design and analysis of many structures and components.
What is Torsion?
At its core, torsion involves a twisting motion. Imagine you’re wringing out a wet towel. As you twist it, the towel undergoes torsion, with different parts experiencing different stresses and strains. Engineers need to understand these forces to ensure structures, like bridges and airplanes, can withstand twisting without breaking.
The Science Behind Torsion
To get a bit technical, when torsion is applied to a material, internal stresses develop. These stresses, called shear stresses, are measured in terms of force per unit area. The material’s ability to resist these forces determines its mechanical integrity. Torsion can cause deformation, which is a fancy word for change in shape, and engineers must predict this to avoid failures.
Everyday Examples
Torsion isn’t just a concept for engineers; we encounter it daily. Take a drive shaft in a car, for example. It’s a long rod that transfers power from the engine to the wheels. As the engine turns, the shaft experiences torsion. Engineers must design it to handle these twisting forces without snapping or deforming.
Another fun example is the suspension bridge. As winds blow across it, the bridge twists slightly. Designers must account for these torsions to prevent collapse, ensuring the bridge remains safe and stable.
Historical Adventures with Torsion
The story of torsion isn’t new. The famous engineer, Leonardo da Vinci, studied torsion in the 15th century while designing machines and inventions. He was fascinated by how twisting forces affected the materials he worked with. This curiosity laid early groundwork for modern engineering practices.
Torsion in Modern Engineering
Today, torsion plays a vital role in various fields:
Aerospace Engineering
Aircraft components, like wings and fuselages, undergo torsion during flight due to aerodynamic forces. Engineers must ensure these structures can handle the twisting, often using lightweight, strong materials like composites to enhance performance.
Civil Engineering
Bridges and buildings are designed with torsion in mind. Earthquakes can apply twisting forces to these structures, so they must be constructed to withstand such stresses, using materials and designs that allow some flexibility without failure.
Mechanical Engineering
In mechanical systems, like engines or turbines, components often spin at high speeds. This spinning generates torsion, affecting the efficiency and longevity of these systems. Engineers optimize designs to minimize harmful effects.
Delving Deeper: What’s Happening Inside?
Imagine a cylinder being twisted. Inside, the molecules rearrange slightly, causing internal stress and strain. Engineers use mathematical models to predict how these stresses affect materials, often employing computer simulations to test designs before creating physical prototypes.
Material Matters
Different materials react to torsion in various ways. Metals may twist without breaking, thanks to their ductility, while brittle materials like ceramics might crack under similar conditions. Understanding material properties is essential for engineers choosing the right materials for specific applications.
Solving Torsion Challenges
Engineers face challenges when dealing with torsion. They must calculate the optimal shape and size for components, considering how they will twist under load. By analyzing factors like material strength and geometry, they can create designs that safely withstand torsional forces.
Future of Torsion in Engineering
As technology advances, engineers continue to explore innovative ways to handle torsional forces. New materials, like advanced composites and alloys, offer exciting possibilities. These materials can provide enhanced performance, helping engineers design lighter, more efficient systems.
The Role of Research
Research into torsion isn’t slowing down. Engineers are investigating how nanotechnology could revolutionize torsional resistance, creating incredibly strong, lightweight components. They are also studying biological systems, like DNA, which naturally withstand twisting forces, to inspire new engineering solutions.
Why Torsion Matters
Understanding torsion is crucial for creating safe, efficient, and innovative designs. Whether it’s ensuring a bridge doesn’t twist too much in high winds or designing a spacecraft that can withstand the rigors of launch, mastering torsion helps engineers solve real-world problems and improve our everyday lives.
Questions for the Curious Mind
Here’s something to ponder: How might engineers use new technologies to further improve structures with respect to torsion? Could artificial intelligence play a role in predicting torsional impacts more accurately? The future of engineering could be full of twists, both literal and figurative, thanks to advances in our understanding of torsion.
By exploring the twists and turns of torsion, engineers craft wonders that withstand the forces of nature and technology, shaping the world with every twist and turn. The next time you twist a rubber band or cross a suspension bridge, you’ll know a little bit more about the power of torsion in making those moments possible.