· Engineering · 5 min read
Process Control: Mastering the Art of Precision in Chemical Engineering
Process control ensures consistent quality in manufacturing. Explore how it brings precision and stability to chemical engineering operations.
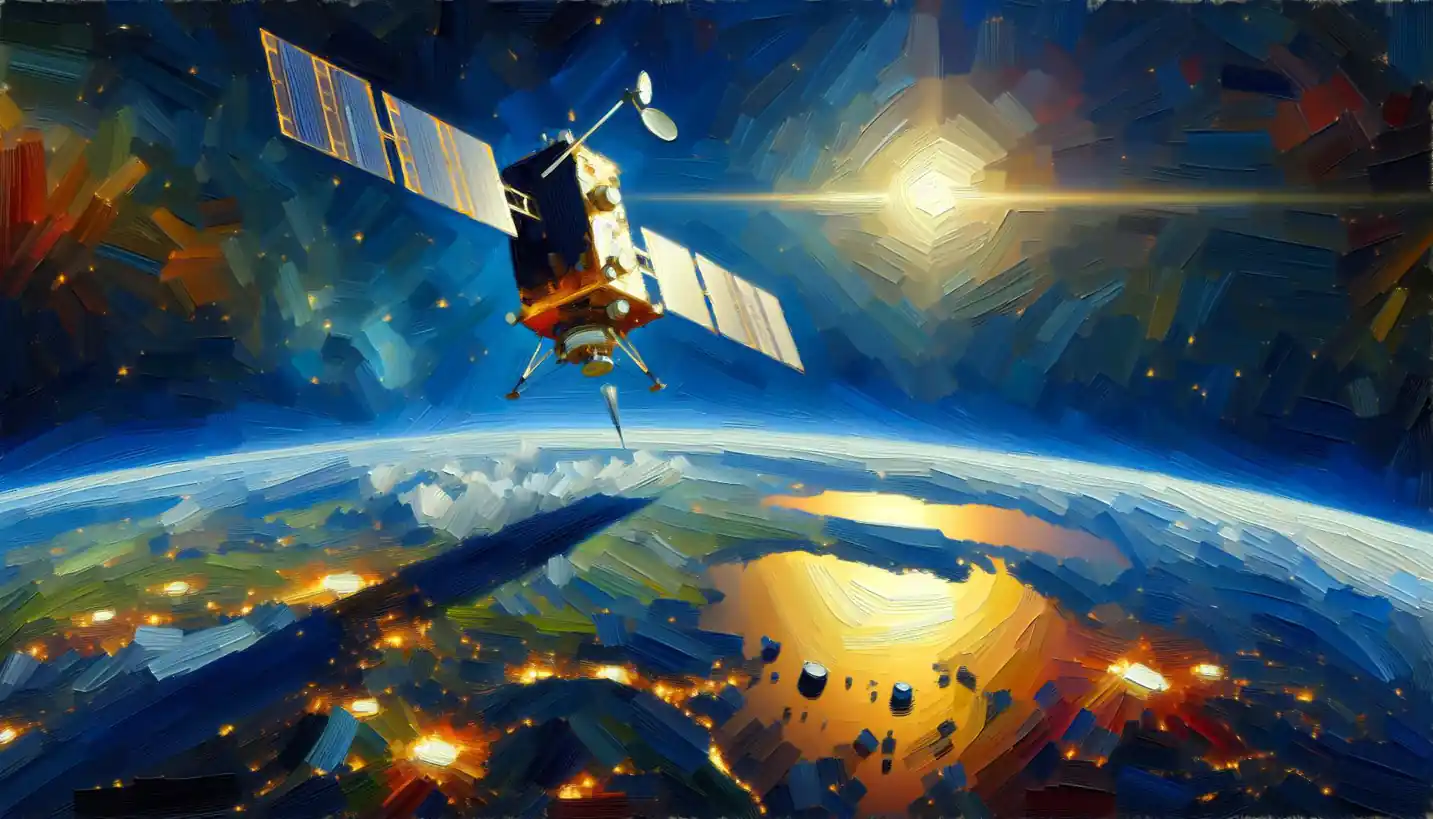
In the bustling world of chemical engineering, there’s a fascinating concept known as “process control.” Imagine trying to bake the perfect cake without any measuring cups or a thermometer. Sounds chaotic, right? Well, process control is like having those essential tools in a vast industrial kitchen, ensuring everything goes smoothly and efficiently.
At its core, process control is all about managing and regulating industrial processes to achieve the desired output. It involves the use of technology and techniques to maintain specific conditions within a plant or factory. Whether it’s the temperature, pressure, or chemical composition, process control keeps everything in check, much like a conductor leading an orchestra.
The Significance of Process Control in Chemical Engineering
Chemical engineering is a field that touches almost every aspect of our daily lives, from the fuel in our cars to the cleaning products in our homes. The processes involved are often complex, requiring precise conditions to transform raw materials into valuable products. This is where process control steps in.
Imagine a chemical reactor, where raw ingredients undergo a reaction to produce something new, like converting plant materials into biofuels. Maintaining the right temperature and pressure is crucial for the reaction to occur efficiently. If the conditions aren’t right, you might end up with an incomplete reaction or even a dangerous situation. Process control systems ensure that these parameters stay within a safe and effective range, just like cruise control in a car keeps your speed steady on the highway.
How Process Control Works
Process control involves several key components working together seamlessly. Sensors continuously monitor the process conditions, providing real-time data on variables like temperature, pressure, and flow rate. These sensors are akin to the taste-testers in that imaginary kitchen, providing feedback on how things are going.
Controllers play a pivotal role as they analyze the data from the sensors. Think of them as the brain of the operation. They compare the current conditions with the desired set points, calculating the necessary adjustments to bring everything back in line. These controllers can be simple devices or complex computer systems, depending on the sophistication of the process.
Actuators are the muscle in this setup. Once the controllers determine what needs to be done, actuators make the adjustments, tweaking valves, heaters, or pumps, much like adjusting the temperature dial on your oven.
Feedback and Feedforward: The Dynamic Duo
In the world of process control, there are two main strategies to keep things running smoothly: feedback and feedforward control. Feedback control is like a reactive friend who steps in when they notice something going wrong. If the process drifts from the desired conditions, feedback control kicks in to correct it, almost like correcting your course if you notice you’re veering off track.
On the other hand, feedforward control is more proactive. It anticipates changes based on what’s coming and adjusts the process in advance. Imagine you know a heatwave is approaching, and you preemptively set your air conditioner to combat the rising temperature. In industrial settings, this might involve adjusting inputs based on expected fluctuations in raw material quality.
The Role of Automation in Process Control
Automation has revolutionized process control, bringing unparalleled efficiency and accuracy. In the past, plant operators had to manually monitor and adjust processes, which was not only time-consuming but also prone to human error. Today, advanced computer systems and software handle these tasks with incredible precision.
This automation allows for real-time data analysis, enabling quick responses to any deviations. It’s like having a highly skilled sous-chef in our industrial kitchen, capable of making split-second adjustments to ensure everything is just right. Automation also aids in predictive maintenance, identifying potential issues before they become problems, much like a smoke detector that warns you of danger before you even see smoke.
Challenges in Process Control
Even with all these advancements, process control isn’t without its challenges. One major issue is dealing with variability. Raw materials often vary in quality, introducing uncertainties into the process. Imagine using slightly different flour brands every time you bake—your cake might turn out differently, right? Engineers must design robust control systems that can handle such fluctuations without compromising quality.
Another challenge is the integration of new technologies. As industries adopt more advanced sensors and AI-driven analytics, compatibility with existing systems can become a headache. Engineers must ensure that new components mesh well with the old to avoid disruptions.
The Future of Process Control
The future of process control looks promising, with innovations like artificial intelligence and machine learning leading the way. These technologies have the potential to further enhance precision and efficiency, offering predictive analytics that can foresee potential issues before they occur.
Imagine a system so advanced that it can learn from past data to optimize processes in real-time, like having a weather forecast predicting the perfect conditions for your cake baking days in advance. This could significantly reduce waste, save energy, and increase productivity, benefiting both the environment and the bottom line.
Why Process Control Matters
The significance of process control extends beyond just efficiency. It plays a crucial role in safety and environmental protection. By keeping processes stable, it minimizes the risk of accidents and leaks, protecting both people and the planet. Moreover, by optimizing resource use, it contributes to sustainable practices, aligning with global efforts to reduce industrial footprints.
In essence, process control is an unsung hero in the world of chemical engineering, quietly ensuring that complex processes run smoothly. As industries continue to evolve and innovate, the role of process control will only grow, becoming more integral in our quest for safer, more efficient, and sustainable industrial practices.
Curious to learn more about how these processes shape the world around us? Dive into the intriguing world of chemical engineering, where precision meets innovation, and discover how these hidden systems refine the world as we know it.